
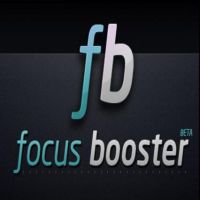
Depending on the feedstock, target yield and product specifications, we tailor our superior steam cracking and ethylene separation technologies to customer-specific demands. Our engineering experts work closely with our customers to optimize every step in this process flow with a view to maximizing return on investment and minimizing energy consumption. The separation train of an ethylene plant is a very complex process sequence. All of which contributes to plant safety. This avoids downtime due to timing issues and prevents the plant from running in the wrong mode. Thermal imaging can be added to provide online measurements of tube temperatures so operators can avoid overheating and hot spots.Īutomatic mode change enables automatic transfer between all operating modes. These simulations give operators key performance and condition indicators, enabling them to fine-tune operations. This means it covers the entire radical chain reaction involved in cracking hydrocarbons containing up to 140 components. Using kinetic modelling, this “digital twin” simulates key performance and operational parameters, calculating more than 2000 possible reactions in the case of steam cracking furnaces, for instance.
#Focus booster crack software#
The Linde Virtual Furnace (LVF) is a set of software modules that model a live furnace based on the design blueprint. These innovations offer various technical and business benefits, resulting in enhanced plant performance overall. In the recent years, Linde has invested substantial effort into the development of digitalization and automation technologies for Linde cracking furnaces and can now offer the most modern and advanced solutions to boost furnace operation and efficiency. Our proprietary technologies utilize the latest coil geometries and metals, proprietary air preheating concepts, next-generation ultra-low-NOx burners and catalytic DeNOx systems to keep emission levels below national and international regulations, maximize yields and minimize energy consumption. In recent years, we have designed cracking furnaces with capacities in excess of 250 kta to meet ever-growing demand for ethylene. Designed to support any feedstock scenario and combination, our furnaces convert raw materials such as ethane, liquefied petroleum gas (LPG), butane, naphtha, atmospheric gas oil (AGO), hydrocracker residue, bio-naphtha, bio-diesel and plastic waste pyrolysis oil with end boiling points up to 580☌ into ethylene and valuable by-products by means of thermal cracking (pyrolysis). Customers also frequently quote highest process safety, ease of operation and robustness as key success factors. Our cracking furnaces deliver outstanding ethylene selectivity, capacity, runtimes and energy efficiency. To date, we have licensed and/or built more than 70 plants around the world. Our offering includes a toolbox and methodology for greenhouse gas emission reductions and improved carbon management to support our customers’ sustainability roadmaps. Our strength lies in providing tailor-made solutions engineered to best meet our customer’s requirements. The highest CAPEX efficiency as well as low energy consumption have always been the focus of our designs. Linde Engineering is one of the few technology contractors worldwide that can deliver technology, engineering, procurement and construction (T-EPC) services for the entire ethylene plant along with downstream units, utilities and offsite units.
#Focus booster crack cracked#
The resulting cracked gas is separated into valuable products such as ethylene, propylene, acetylene, butadiene, pyrolysis gasoline and BTX, all according to the specifications required for downstream processes. They involve cracking hydrocarbon feedstocks in the presence of steam and at temperatures of between 800° and 870☌. Steam crackers are large and complex units at the heart of petrochemical complexes, producing the important building blocks ethylene, propylene, butadiene, aromatics and acetylene.
